portfolio
Currently, Mercedes-Benz remanufactures engines, gearboxes, cylinder heads, oil pumps for trucks and buses. In a gearbox, up to 65% of its parts can be recovered, while in an engine, up to 55%. For this, a diagnosis is made and the parts that can be reused are evaluated.
The advantages: an economic saving of up to 50% compared to the purchase of a 0 km part, the same Mercedes-Benz guarantee and the same final durability. Also, as availability is immediate, the customer avoids stopping the vehicle for longer than it takes to schedule a visit to the workshop.
“Customers received it in a spectacular way, it was a new aftermarket alternative for cargo and passenger transport vehicles. Normally engines and gearboxes were repaired in a different way. The remanufacturing concept generates a cost benefit for the customer compared to a traditional repair. Mercedes-Benz quality is maintained in the same way as a 0 km part, with the same guarantees”, said Rivero.
The process is very simple: the customer shows up at the dealer for a repair or through a scheduled visit for estimated wear. “The technicians make a diagnosis simultaneously with the client. It allows defining a repair to be carried out and the time. Once accepted by the customer, the gearbox or engine is already in the dealer’s stock. With which, time is reduced and that damaged part that is disassembled is sent to our industrial center to enter the remanufacturing cycle. It is an advantage for the customer, because he leaves the dealership with his truck or bus repaired in record time”, says the manager in charge of after-sales.
Therefore, before mechanization, the work team is central, since it is an artisanal process, where the key is the knowledge and ability of the operators. “With the right equipment and machines, we maintain Mercedes-Benz quality and the factory warranty,” adds Rivero.
sustainability
At Mercedes-Benz they separate the process into two aspects. One is the benefit to the customer in repair time and costs. But they also highlight the environmental contribution through the reuse of materials: 65% is remanufactured, which implies a reduction in energy consumption and raw materials. Waste and waste are less, in a concept that is based on the circular economy.
Reman contributes to reducing pollution by disposal and the use of resources in the manufacture of a new product. According to TÜV SÜD, a company of German origin specialized in certification, testing, auditing and training, it is estimated that the savings obtained with a remanufactured box is approximately equivalent to the CO2 absorbed by 11 trees in 10 years of growth.
After starting the operation in 2017 with boxes, the remanufacturing was later extended to Euro 3 and Euro 5 engines. “We are very proud, we could only have achieved it with Argentine work. The skilled labor on this project was the difference in reaching this important milestone. This reaffirms the commitment to continue betting and investing in our national production”, concludes Rivero.
Source: Ambito
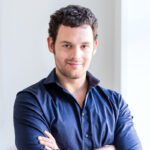
David William is a talented author who has made a name for himself in the world of writing. He is a professional author who writes on a wide range of topics, from general interest to opinion news. David is currently working as a writer at 24 hours worlds where he brings his unique perspective and in-depth research to his articles, making them both informative and engaging.