In the middle of the decade, Volvo wants to revolutionize production and drastically reduce the work steps with the launch of the first purely electric platform. Mega Casting is a manufacturing technique that Tesla also uses in the production of its vehicles.
Mega Casting is not a new television show in which Dieter Bohlen sits on the jury and more or less talented singers perform a song. Rather, it is about a manufacturing process in which large aluminum parts are made in one piece. To do this, liquid aluminum is poured into a tool and then pressed into the appropriate shape at an extremely high pressure of 8,000 tons. A water bath accelerates the cooling process before the component is finally cut to size and the edges are straightened by laser. An advantage of this method is that there is significantly less material waste than with traditional pressing tools. Volvo wants to use this process from 2025 at its main plant in Torslanda, where a vehicle will then roll off the assembly line on a new, purely electric platform.
“So that this effort is also financially worthwhile, as many parts and functions as possible must be combined in this element,” explains Mikael Fermér, the project manager for the introduction of Mega Casting, the procedure to drastically reduce the complexity of production. In addition, with Mega Casting, the limits of platform thinking should be a thing of the past, since elements of different sizes and shapes can be produced without great effort. Reacting to technical advances and structural differences, such as in the electric motors, is much easier than before and can even be carried out during production or the life cycle of a car.
Such large components as are produced in Mega Casting can only be transported with great effort. Therefore, if you want to reduce logistic costs, the manufacturing has to take place close to the main production line. Tesla also relies on mega casting and combines 70 parts in one during production, which Volvo wants to top. “We are aiming for a ratio of 100 to one,” clarifies Mikael Fermér. Each of the Mega Casting tools is around 20 meters long, six meters high and six meters wide. The clocking will amount to 140 seconds per component, in order to produce 60 units per hour, several machines are needed. The metal isn’t off the peg either: the Swedish car manufacturer uses so-called F-temper aluminum for this production step, which does not have to be post-treated with heat after casting.
The positive consequences of this manufacturing process are manifold: The number of components is reduced, production and last but not least the design are more flexible. The environment also benefits from mega-casting: the energy consumption is significantly reduced, the CO2 footprint is reduced, as is the weight of the car and, according to Volvo, more recycling materials can also be used. Volvo currently assumes 50 percent recycled materials. “The goal is 100 percent, but these materials still don’t have the quality that we imagine”; says Mikael Fermer. Volvo wants to make the suppliers responsible and only use aluminum whose production requires less than four kilograms of CO2 per kilogram of metal. Speaking of weight: Compared to a steel component, the aluminum version is said to be around 15 to 20 percent lighter. Mega Casting is a key part of manufacturing the first all-electric vehicle platform. The first component to be manufactured in this way is the rear floor assembly.
This is not the only measure in Volvo’s car production of the future: Volvo is investing around one billion euros to make the Torslanda main plant fit for the next generation of electric vehicles from the middle of the decade. In addition to the body and the floor assembly, the battery is a central component of every BEV. In a modern factory, the battery modules are assembled into battery packs. The production of batteries for plug-in hybrids serves as a blueprint, but this principle is now being used for significantly larger energy storage systems. A new battery assembly facility will also be introduced at the same time, with the battery modules being integrated directly into the vehicle’s floor structure. A new paint shop will also be put into operation so that sustainability is done and the number of cars get the right color. With the overall concept, it almost goes without saying that this is done as resource-saving as possible (how).
Source: Stern
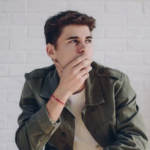
I am a 24-year-old writer and journalist who has been working in the news industry for the past two years. I write primarily about market news, so if you’re looking for insights into what’s going on in the stock market or economic indicators, you’ve come to the right place. I also dabble in writing articles on lifestyle trends and pop culture news.