interview
An IT malfunction temporarily paralyzed production at VW. Heiko Weber from the consulting firm Berylls believes that something like this will happen more often. The dependency on IT systems is extremely high and a failure costs manufacturers a lot of money
How can something like that happen?
It is to be expected that things like this happen. We will see this often in the future. All processes in production and the associated supply chain are very complex. The consequence of the consistent digitalization of these processes is that the dependence on all of these IT systems becomes so great that a failure can hardly be controlled. Such a failure can arise, for example, from a routine process in which something was not taken into account. Human error is usually involved. You can say: Never touch a running system: If I don’t do anything, then things will run. But of course you have to do something regularly and that increases the risk.
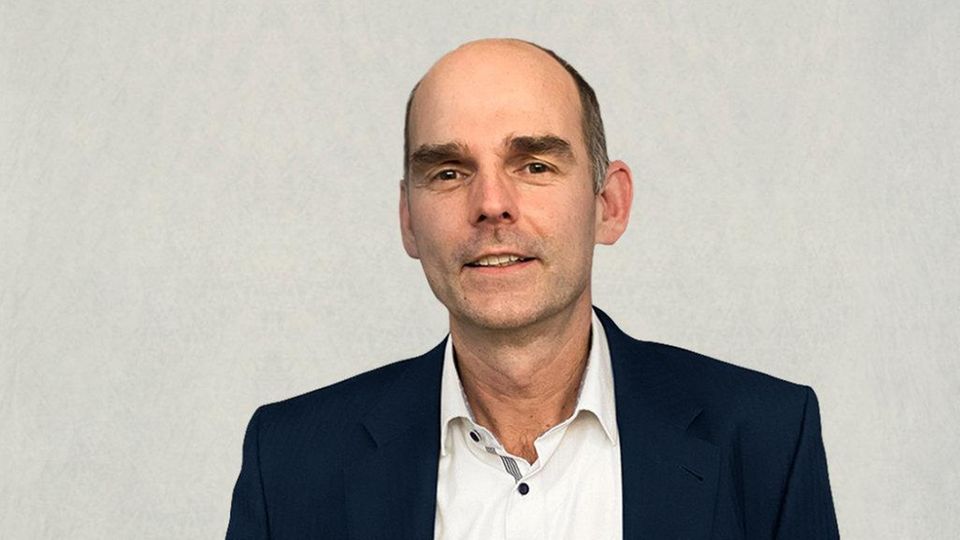
Is the auto industry particularly sensitive to such failures?
I consider the automotive industry to be a leader in the digitalization of production networks. Networks mean that car manufacturers integrate suppliers, logistics and maintenance service providers into their IT systems. Car production is so highly digitalized because car manufacturers’ demands for efficiency and perfection are particularly high. This means that the systems are very complex.
So complex that they can no longer be controlled?
I do not believe that. Car manufacturers are very careful with everything that is introduced in terms of IT technology. The systems are thought through in many places and by many people involved. If you now ask the question whether this goes so far that the systems become inscrutable, then that is probably the case. Such a system is no longer transparent for a single person. This doesn’t have to have apocalyptic consequences. But it is a huge challenge. And an incident like the one at Volkswagen must always be an opportunity to learn from it.
Is such a glitch an indication that a system is fundamentally designed incorrectly?
I don’t see that. I still consider well-done end-to-end digitalization to be one of the most important levers if the auto industry wants to improve.
How fatal are the consequences of such a breakdown?
They are not fatal, but they are definitely extremely expensive. You just have to estimate how many thousands of cars cannot be built. Billions of dollars can come together. It is not so easy to catch up on the number of units that have been lost. This may be a little easier at the moment because many plants are not at capacity, but an additional weekend shift can actually recoup a lot at the moment.
You said the company should learn from this. How?
Analyze the cause or causes, install backup systems, change processes. These can be hardware measures. There may be regulations that require you to carry out certain checks before a software update, for example. It can also be software protection, in which software carries out certain checks automatically.
Are more investments necessary for secure IT?
Car manufacturers are already investing a lot in IT and expanding digitalization. I have the impression that they are very aware that they have to invest a lot here.
Like Toyota a few weeks ago, Volkswagen has stated that there is no evidence of an attack from outside. Nevertheless, the question arises as to whether the failures show how vulnerable the IT systems are to cyber attacks.
The events show how incredibly dependent car production is on functioning systems. Because the risk is so high, the risk of an external attack is also high. Cybersecurity is one of the most important challenges automakers face right now. They are well aware of this danger.
If the breakdown occurs – what can you do to repair it quickly?
The fact that it only took half a day for VW to get the problem under control suggests that it was a problem in a central system – not a bug from the periphery that propagated. And that the company reacted quickly. In any case, internal IT resources that understand the system are important. Here you can’t just rely on service providers. At the same time, you need service contracts that ensure that the IT companies are available at all times. Certainly at least 30 to 40 people at VW had sleepless nights. But – as in all crises – I also need a strong task force in the top management that understands the situation and organizes the response to it.
At least that’s what many companies have practiced during the crises of the past three years. Do you have the impression that resilience and crisis response are working in the auto industry today?
Certainly not yet universal, especially at the middle levels there is still the illusion that one will return to the quiet life of before. But it has reached the management levels. The people we deal with are very task force tested. There is no one left who believes that the old ways of working will apply again in two years.
However, good crisis response does not necessarily give the company a competitive advantage.
That’s right, reacting quickly to risks is unfortunately a must-have. But if I don’t master this, I’ll soon be out of the window. However, if as a manager I am able to quickly switch to crisis mode, then that gives the company agility and flexibility. And these in turn also pay off in competition.
This article first appeared on
Source: Stern