Anyone who thinks that the corona pandemic no longer has the auto industry in a tight grip is seriously wrong. Even if many corporations celebrate record orders, the supply chains are still not working.
The same picture every week – for months. Time and again, production in the large car plants in Europe, Asia, South America or the USA stops – sometimes for a few days or even a few weeks. Different models cannot be manufactured at all, because the better equipped or equipped with high-tech the vehicle, the more important the missing chips are. The demand is greater than ever. Global car production rose by around 15 percent in the first quarter of 2021 and by the end of the second quarter, the IHS analysts expect growth of around half compared to the markedly weak period of the previous year. But while the automotive industry has slowly recovered from the pandemic and demand is adjusting, it continues to face a number of constraints in the supply chain. On a daily basis, the OEMs and suppliers’ crisis teams evaluate the resilience of supply chains and stocks and adjust production and schedules almost in real time.
“The first major disruptions occurred in the first quarter when it became clear that the supply chains were no longer in sync and the semiconductors were no longer available to meet the increased demand for vehicles,” said IHS analyst Mark Fulthorpe, responsible for global Passenger and light vehicle production, “Semiconductor shipments had shifted over time to other industries, consumer electronics, and demand for vehicles had declined sharply in Q1 and Q2 of 2020 after the initial disruption from COVID-19.” But that strong demand also created an imbalance as the semiconductor supply chain was not designed to meet the level of emerging automotive demand. IHS analyst Phil Amsrud: “As a result, an estimated 1.4 million light vehicles worldwide were not built in the first quarter.
At the beginning of the second quarter, the disruptions continued to affect the supply chains in the automotive industry, especially in the area of semiconductor technology. The tense situation from the first quarter was exacerbated by the effects of severe storms that swept Texas. Shortly thereafter, other supply chains were severed by the earthquake in Fukushima, Japan, and the fire at Renesas’ Naka 3 plant. The effects made themselves felt more painfully than ever for many brands, especially in the second quarter of this year.
IHS expects further disruptions in the third quarter, but not to the same extent as in the first half of the year. “We expect an improvement because there is a better understanding of the situation and great efforts are being made to improve transparency within a very complex supply chain,” explains Phil Amsrud. “We see evidence of this in some of the more relaxed announcements from General Motors that to resume operations earlier than originally planned and in Toyota’s continued commitment to the planning. ” Toyota, for example, has been monitoring the supply chains since the earthquake and the corresponding tsunami in Fukushima ten years ago, while other manufacturers go to much less effort to monitor the processes meticulously.
The IHS experts assume that this, together with the restoration of semiconductor capacities at Renesas in Japan and NXP and Infineon in Texas, can ease the current still tense production situation. As before, the European car manufacturers have to repeatedly suspend the production of individual models and special versions. The dealers phone thousands of customers whether they can do without special equipment variants so that the vehicles can be delivered earlier. The situation around semiconductors will only improve slowly and hardly any car manufacturer has any doubts that the problems will extend well into 2022.
The factories that were hit by the storm in Texas and the fire in Japan are only slowly returning to their pre-crisis production levels. The most recent fire in the 300 mm clean room at Renesas’ Naka production facility in Japan only affected a small area of production, but damaged the water supply, the air conditioning and the production facilities themselves. Since June 25, Naka 3 has been back to one hundred percent its production level before the fire. NXP also announced that the production facilities in Austin are running at full capacity again. In response to the disruptions, many semiconductor suppliers are expanding the window for firm orders from the previous 12 weeks to now a year or more. Some minor adjustments are allowed, but the orders become non-cancellable orders, meaning the customer is responsible for the value of the entire order even if demand falls.
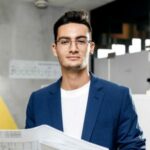
I am Pierce Boyd, a driven and ambitious professional working in the news industry. I have been writing for 24 Hours Worlds for over five years, specializing in sports section coverage. During my tenure at the publication, I have built an impressive portfolio of articles that has earned me a reputation as an experienced journalist and content creator.