In full era of automated systems and artificial intelligence (AI), Many small and medium enterprises, for different reasons, continue to use manual management to carry out their operations.
In some cases this occurs because they support traditional forms of work, which have allowed them to grow in the past, in others due to new alternatives or difficulties to adapt to change.
However, this method significantly increases the probability of errors due to the lack of standardization and automation.
While the probability of making mistakes is wide, we can cite some cases, usualhow to incorrectly record the name or amount of an input delivered by a supplier. An automated system would avoid this mistake by having previously charged information and only require the selection of the correct amounts.
On the other hand, lack of centralization generates outdated or uncoordinated information problems between different areas.
A typical case would be to register the sales of a product, such as a certain taste of ice cream, in a form and the stock in a different one, making it difficult to detect the need to make an order to the supplier.
With a centralized system, the information is automatically connected, allowing alerts to be generated that prevent stock breaks and improve operational efficiency.
On the other hand, a lot of time is lost when manual records are repeatedly made on the same inputs, products, suppliers or customers that are part of the daily operation of a business. This type of records implies writing and writing down identical information over and over again, which is not efficient.
On the other hand, an automated scheme eliminates this redundancy when pre-configuring the information that the business uses regularly, leaving space only to record the modifications.
For example, if the same request for an input is made every month in a fixed amount to a usual provider, the manual record of that information is unnecessary. With a system, the order is previously configured and, with a single click, it can be processed, thus saving time and effort.
In fact, many companies before conducting stock manual counts every day and collected paper remitting to add consumption, in order to estimate the use of their products and plan production.
With an automated system, they now perform the inventory only once a week, while the rest of the movements are automatically managed thanks to a complete traceability of the information throughout the company.
In manual or Excel efforts, it is common for certain tasks to be overlooked or that important data is not recorded because you do not have adequate hand support at the time. For example, not having a good platform, you can miss the monitoring of the key details about a collaborator.
On the contrary, with an online management system, all profiles and cards of the employees, presentism registration, licenses, signatures, etc. can be loaded loaded.
Another aspect to highlight of the platforms is that the integration of information allows obtaining value of the data through different analysis modules. In that sense, having all the data in the same place is essential to analyze them and draw conclusions in the future.
In short, the acquisition of this type of instruments will be essential for SMEs to improve decision -making and operational efficiency for the future. While it is true that many have managed to grow manually handling, in that way they are exposed to many errors and losing opportunities of greater evolution.
Devfactory Founder and CEO
Source: Ambito
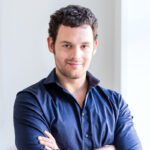
David William is a talented author who has made a name for himself in the world of writing. He is a professional author who writes on a wide range of topics, from general interest to opinion news. David is currently working as a writer at 24 hours worlds where he brings his unique perspective and in-depth research to his articles, making them both informative and engaging.