Dirk Harbecke, CEO of Rock Tech Lithium, is building a so-called lithium converter in Brandenburg. He says Germany has some of the best chemical know-how in the world.
Battery storage is one of the key future areas of the economy in China. The People’s Republic has built up a continuous value chain from raw materials to finished battery cells because Beijing has recognized that there is no e-mobility without batteries; Electricity from wind and solar systems needs storage to compensate for the fluctuating yield; Without storage, solar power runs out as soon as the sun goes down. Europe must catch up in this area if it does not want to become dangerously dependent.
Europe needs access to lithium
Although battery factories are being built in the EU, it is just as important to secure relevant lithium deposits. Rock Tech Lithium exploits a mine in Vancouver and builds the first lithium converter in Germany. The mined metal is processed and refined so that it can be used for battery production. A start has been made.
Mr. Harbecke, battery technology plays a central role in the climate-neutral energy transition. EU Europe has to catch up – in all areas of battery production, such as the extraction of raw materials such as lithium and processing. Where is Europe currently?
Active work is being done in Europe to build up the battery value chain. Battery production is still predominantly carried out by Asian manufacturers. The first lithium production in Europe lies in the future. Therefore, the processing and recycling of lithium, Rock Tech’s focus, is important for building a European value chain right now.
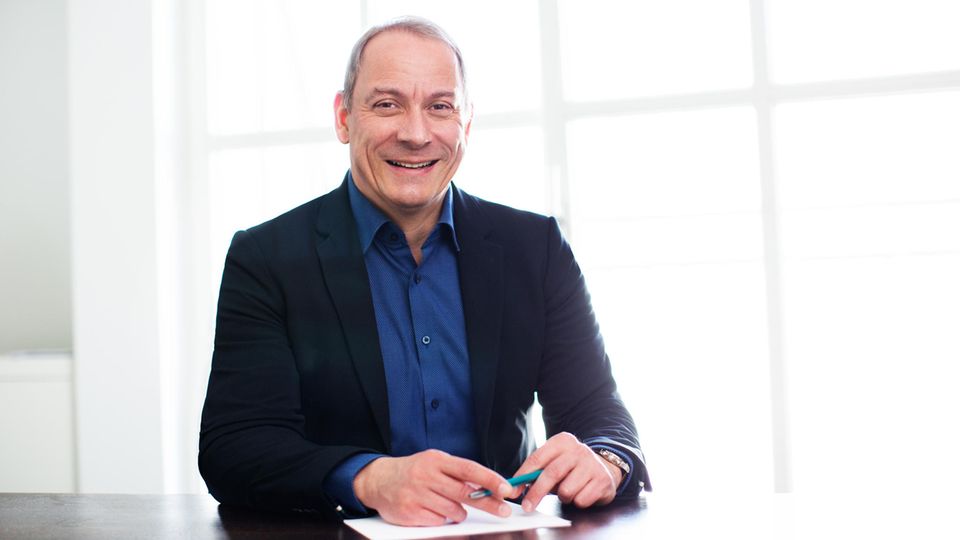
There is resistance to lithium mining in Serbia. How will it be mined and what will the landscape look like later?
We do not have sufficient information about Rio Tinto’s specific expansion plans in Serbia. Provided that the highest social and ecological standards are adhered to when mining the local lithium reserves, we fundamentally support the local extraction of critical raw materials.
The extraction of raw materials is important in order to build up a stock of batteries. But how much raw material does a battery ultimately use and how much can be reused?
For a battery with an energy density of 250 watt hours per kilogram (Wh/kg), the total mass of the battery required to store one kilowatt hour (kWh) of energy is 4 kilograms. This is distributed approximately 60 percent on the cathode and 40 percent on the anode. Let’s break down the cathode (about 2.5 kilograms). These are lithium (Li) 6 percent or 150 grams, nickel (Ni) 75 percent or 1850 grams, manganese (Mn) 10 percent or 250 grams, cobalt 10 percent or 250 grams. For the anode, a total of 1.6 kg can you can’t say that across the board. All raw materials mentioned can be completely recycled and returned to the cycle.
New technologies extend the lifespan of batteries and accumulators. Is there any concern about battery death? Cars unfounded? What framework do we have when it comes to service life and charging cycles?
The fear of battery death in cars is unfounded. The numbers from a large electric car manufacturer speak for themselves. According to the Tesla Impact Report 2023, the average battery capacity loss for Model 3 and Model Y after 200,000 miles is 15 percent. The numbers are similar for the Model S, which is already over ten years old. We assume that newer battery systems in BMW and Mercedes vehicles, for example, will maintain their range even better. After full-load operation in vehicles, these batteries can continue to serve as a second use in battery storage systems.
When we hear the word battery, we first think of e-mobility. In order for renewable energy to work, the green electricity must be stored. When will large storage facilities be built in the EU? How do you assess the need?
In its communications, the EU assumes that around 200 gigawatts of storage capacity will probably be required from 2030. Today there is about 60 gigawatts of capacity. The target for the production of green electricity from 2030 is a capacity of one terawatt, i.e. 1000 gigawatts in Europe. This means that storage should be available for 20 percent of the energy generated.
Storing electricity, whether mobile or stationary, is a crucial key technology. Does the EU have a chance of keeping up with Asia and the USA here? What needs to be improved?
Europe has the potential to compete with Asia and the USA. Realizing this potential requires massive investment in research and development, real political commitment and a strong commitment from major energy suppliers and car manufacturers.
They are building a lithium converter in Brandenburg. In simple words: How does such a system work and what are the challenges?
The overall process can be summarized as follows: The raw material spodumene concentrate is heated, ground and roasted, which creates lithium sulfate. Lithium hydroxide is then produced by adding chemicals, separating precipitation products and concentrating the solution. In the final production step, lithium hydroxide suitable for batteries is created through crystallization and drying. Challenges in production include logistics, continuous assurance of product quality and purity and utilization of by-products.
When do you expect production to start?
We will begin construction of the Guben lithium converter at the beginning of 2025. The construction phase will take approximately 24 months. We assume that we will start ramping up the plant during the construction phase and will therefore be able to produce battery-compatible lithium hydroxide in the first half of 2027.
To what extent does such a converter help to differentiate oneself from countries like Australia? The EU has goals – 40 percent of the demand should be produced domestically, how many plants are necessary for this?
As the basis for a true circular economy, Europe needs its own lithium converters in order to be able to access lithium that is produced safely and in an environmentally friendly manner. In order to be able to cover its own needs from recycling sources, Europe will need around ten such converters by the early 2030s.
Your mine is in Ontario, why are you building your plant in Germany of all places?
Germany has one of the best chemical know-how in the world, a strong customer base in the automotive industry, for example, the highest environmental and safety standards and an internationally recognized and respected approval process. This means that our converter project in Guben can serve as a blueprint for further rock tech projects in other countries. We are building the second lithium converter in Canada.
Source: Stern