To achieve continuous improvement, all members are invited to give their opinions or contribute ideas, achieving a collaborative and team work environment.
In the 50’s, Taiichi Ohno He returned surprised from his trip to the United States. He saw how the shelves of large supermarkets were never empty, since they were replenished with products in the necessary quantities and at the necessary time. All these observations led him to think about how this methodology could be applied to Japanese factories, where what is not surplus, precisely, is space. Thus arises one of the most revolutionary production methods in history, known as the “Toyota Production System”.
The content you want to access is exclusive to subscribers.
The first thing that supports this change are some values such as Genchi Genbutsu (go and see), that is, commit and go to the source; kaizen or continuous improvementnot settle for achievement; challenge, teamwork and respect. Ideas popularized mainly by the Toyota car factory, where the system is only put into operation after the customer places the order, the necessary parts arriving at the process just in the time they are needed. In this way, unnecessary stocks that hide inefficiencies are eliminated.


Kanban cards were developed as an information system to give notice that a component is running out and must be supplied. The time required to produce a unit is recorded, which is called “takt time”and is carefully monitored with Heijunka, a program to prevent setbacks or unforeseen events on the line regardless of the product being manufactured. Efficiency is created, not just measured. Reducing useless processes or wasted time is reducing Mudas; and by eliminating them, efficiency is increased.
Contrary to what happens in our culture, where problems are hidden or concealed for fear of sanction, with Jidoka, anomalies become visible, authorizing any member of the company to stop the process. The problem is displayed on a board for everyone to see and team members are encouraged to examine its causes to make Genchi Getbutsu or go to the source and eliminate the causes of the problem. Things are not done according to each person’s criteria, but everything is standardized, ensuring that it is done according to a standard. In this way, we think about quality and customer satisfaction, ensuring a greater return on investment for investors.
The 5S method to achieve continuous improvement
To achieve continuous improvement, all members are invited to give their opinions or contribute ideas, achieving a collaborative and team work environment. There is a total commitment of each employee to their work. Your opinions matter. Employing the 5S –order (seiton), classification (seiri), cleanliness (seiso), standardization (seiketsu) and maintaining discipline (shitsuke)– A clean and orderly work environment is achieved that benefits the entire production process. Caring for the environment is also a value, and is achieved by manufacturing products with minimal impact, as well as safety, where safe and healthy work environments are ensured.
We live in constant change, where the phrase “there’s no money” and “You cannot spend more than you collect” It has become common. Taking these ideas to the State could perhaps allow you to generate some savings. Furthermore, let’s imagine this institution as one where the service that is needed is provided in the quantity and at the time that it is required. Applying 5S within would mean having order, cleanliness and standardization in dependencies that accumulate and do not seek efficiency.. Showing the problems instead of hiding them would be a relevant cultural change to make the functioning of the public transparent, as well as improving the resources available.
Productivity is measured as the ratio between the results obtained and the resources used. Therefore, if the same results are obtained using fewer resources, or more results are obtained with the same resources, the productivity of the State can be increased. This does not necessarily imply getting rid of personnel, but rather eliminating unnecessary movements, delays, storage and useless operations, thus contributing to improving the quality of public service without making large investments, only working to improve administration.
In times of crisis and scarcity, small ideas could generate big savings. And those savings will be used for better uses or applications to improve the quality of life of all citizens.
Entrepreneur and Professor at the Faculty of Engineering and Exact Sciences of UADE.
Source: Ambito
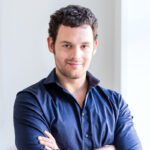
David William is a talented author who has made a name for himself in the world of writing. He is a professional author who writes on a wide range of topics, from general interest to opinion news. David is currently working as a writer at 24 hours worlds where he brings his unique perspective and in-depth research to his articles, making them both informative and engaging.